


Also, exceeding Ipeak demagnetizes the motor magnets.
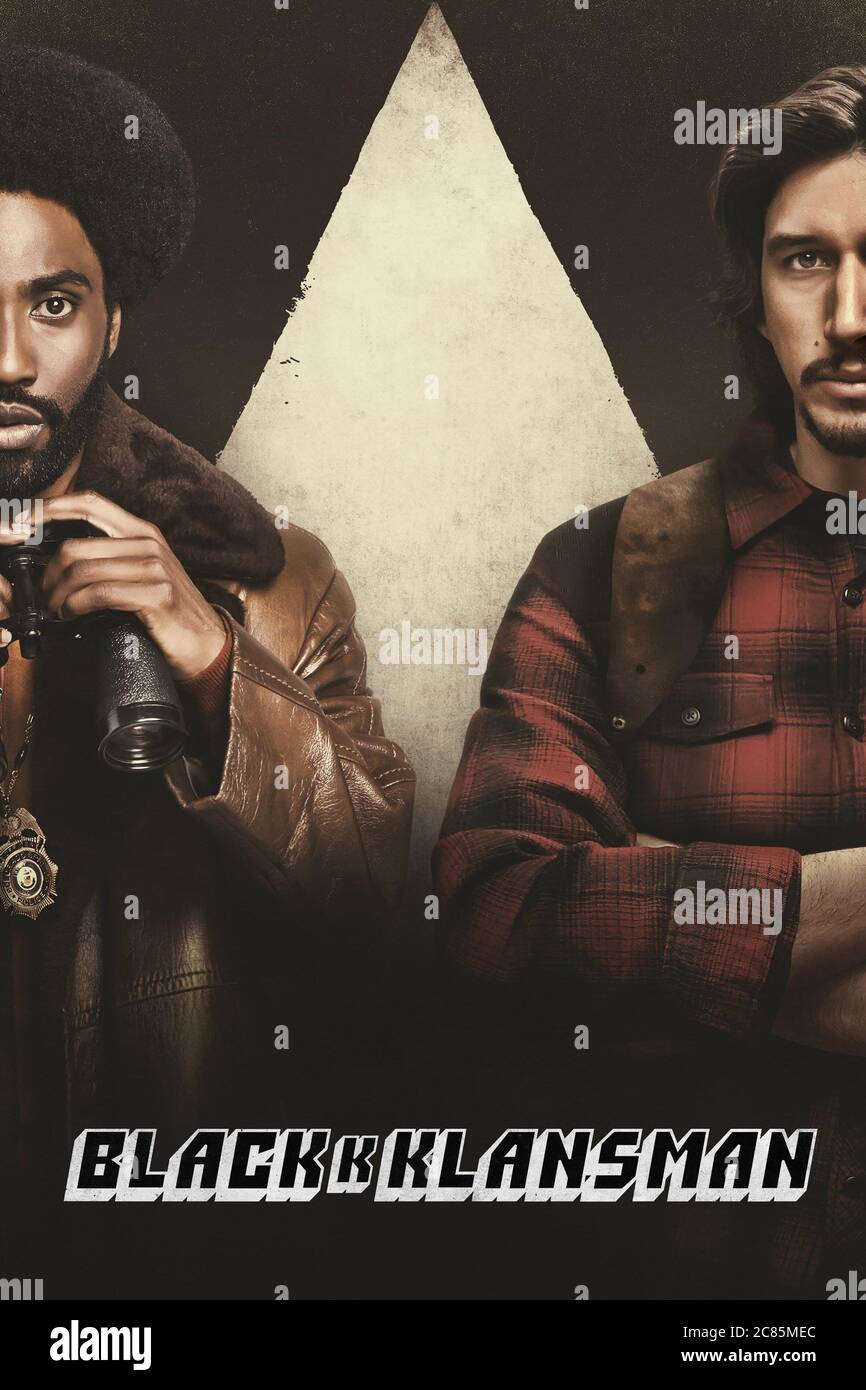
Sustaining Ipeak for excessive periods harms the motor because it develops high temperatures.
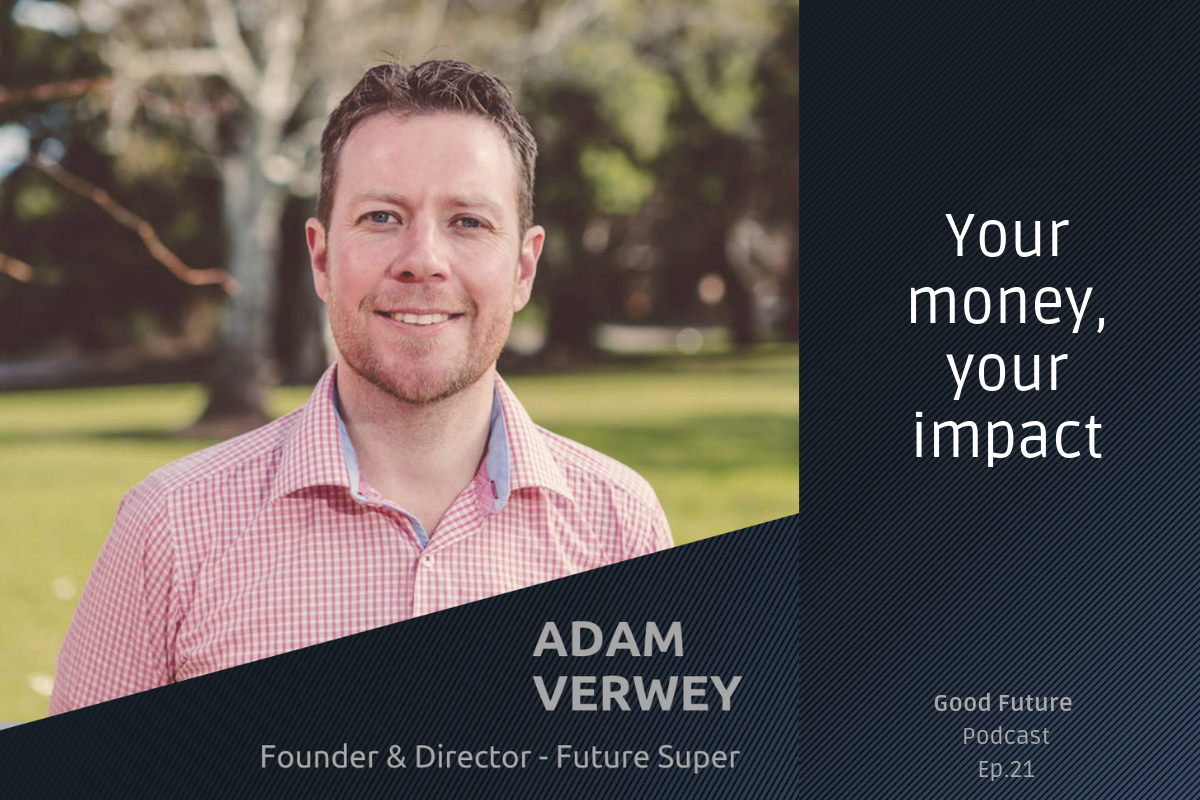
In Equation (2), the current I can have a maximum peak value Ipeak which produces a peak torque Tpeak.
#ADAM JOHN DIRECTOR SERIES#
Z = Effective number of series conductors per coil Motor torque is directly proportional to the developed current in the armature windings thus: In other words, there will be limits to the motor’s ability to meet the desired load points. The designer also designates a maximum safe speed for the motor, usually depending on its rotor diameter or, if it is a brush-type motor, on number of commutator segments. The maximum current also limits the amount of output-shaft torque the motor can produce. Because the initial heat rise usually comes from armature current, this automatically sets a maximum current permissible in the armature windings for a given time. The new winding must not compromise the maximum safe temperature for the given motor size. There are limitations in power output capability in terms of torque, or speed, or both. DC motor ratings depend on the motor’s ability to dissipate the heat created by the losses without exceeding its maximum operating temperature. The difference between P in and P out constitutes the motor losses. Conversely, a higher speed at the same power output means a torque change inversely proportional to the speed increase.ĭue to inefficiency, not all of the power input, P in, to a motor becomes power output. To begin, let us define motor power output as the product of torque and speed measured at the motor shaft for a specific load point, that is:Įquation (1) shows that, to get the same continuous power output at a higher torque, you need only a proportional reduction in speed. We must revisit some of the figures of merit that dominate dc motor design the definition of motor parameters affected by winding changes and their intrinsic relationship. The procedure is simple once you define the “load points.” On the basis of the applications, each load point is defined by the torque and speed the servomotor needs to do its tasks. A winding change is nothing more than a new combination of number of coil turns and magnet wire gage. It would help motor users much to have a way to quickly calculate new motor parameters and assess their effects on the servo system. This file type includes high resolution graphics and schematics when applicable.Īn armature-winding change affects many parameters, including the torque constant K t, voltage constant K e, armature resistance Ra, and armature inductance L a. Or, because of hardware economies, an OEM designer of short-run or single-unit customized machinery may prefer not to change motor physical characteristics, but needs to change performance characteristics to suit individual applications. For example, in a retrofit use, the motor’s envelope and footprint might already exist, but the performance characteristics no longer fit. Increasingly, equipment designers who use dc servomotors find that they need customized motor windings to match specific applications.
